Suntory to make fossil-free PET bottles from waste and residues like used cooking oil
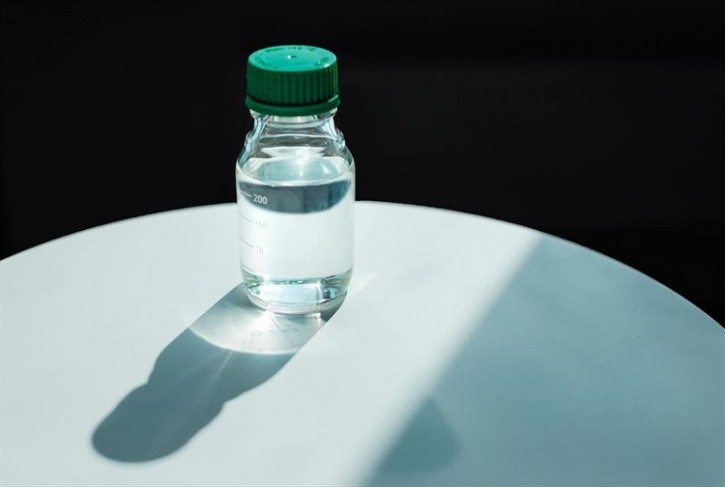
PET (polyethylene terephthalate) is a type of clear, strong, lightweight plastic. It is the preferred material for plastic bottles. But like most plastics, new PET is predominantly synthesised from fossil hydrocarbons - although PET bottles in many regions come with high collection and recycling rates.
Developments in hydrocarbon production technology mean it is now possible to produce PET from bio-based materials.
This is what Finland-headquartered Neste, a supplier of renewable fuels and feedstock for plastics, will be doing for the first time with its renewable feedstock Neste RE in collaboration with Japanese oil and energy company ENEOS, Mitsubishi Corporation, and beverage major Suntory.
ENEOS will use bio-intermediates based on Neste RE to produce bio-PX (Bio-Paraxylene) at its Mizushima Refinery in Okayama, Japan. The bio-PX will then be converted to PTA (Purified Terephthalic Acid) and subsequently to PET resin for Suntory to use to manufacture their PET bottles. Mitsubishi Corporation will be coordinating the collaboration between the value chain partners.
A mass balancing approach will be applied to allocate the bio-based feedstock to the PET bottles, which will be used by Suntory for its products in 2024.
How is a renewable feedstock for PET made?
Neste is using bio-based materials such as waste and residue oils and fats and turning them into renewable fuels and raw material for polymers.
Raw materials for Neste include used cooking oil, vegetable oil processing waste and residues, for example palm fatty acid distillate, spent bleaching earth oil or palm effluent sludge. Others include tall oil based raw materials, technical corn and animal and fat fish wastes from food processing.
In the mid- to longer-term, Neste expects to introduce novel vegetable oils derived from advanced, more sustainable agricultural concepts to its raw material portfolio.
“Our Neste technology allows us to turn renewable raw materials into pure hydrocarbons that can then be used in the existing plastic value chains and infrastructure,” explained Lilyana Budyanto, head of sustainable partnerships APAC at Neste Renewable Polymers and Chemicals business unit.
This is the role of Neste’s renewable Neste RE. Being ‘drop in’ feedstock means that it can be used to replace fossil feedstock in the production of all kinds of plastics without the need to change the infrastructure.
While Neste RE can and has been used in value chains for polypropylene, polyethylene or other polymers, the cooperation with Suntory marks the first time renewable Nestle RE is being used for the production of PET. “We believe this project to be among the first instances of fully renewable PET in general,” Budyanto told this publication.
Decarbonising production with renewable feedstock for PET bottles
Other non-PET applications are also running across the US, Germany and Japan, amongst other geographies. In the US, McDonald’s has been using renewable polymers for clear cups, and in Japanese supermarkets it’s possible to buy onigiri or noodles wrapped in polymers made from renewable Neste RE. In Germany, Tchibo is also using them to make coffee capsules.
A major benefit for food and beverage companies is that polymers based on Neste’s feedstock are ‘completely the same’ as those from conventional materials when it comes to properties, quality or safety, according to the company.
Yet, they come with a much lower footprint. As in the case with the Suntory collaboration, the renewable feedstock replaces fossil feedstock in the production of PET bottles. “This will lead to a decrease in the dependence of fossil resources and an improved carbon footprint for the PET bottles,” Budyanto told this publication.
Neste’s own life cycle assessment (LCA) for Neste RE – the feedstock only, not including further value chain steps up to the final PET application – suggests it reduces the carbon footprint by more than 85% when replacing fossil feedstock.